当前电站锅炉吹灰普遍根据运行规程定时吹灰,未考虑负荷、煤质变化对受热面灰污状况的影响。针对锅炉灵活运行、燃用非设计煤种时,吹灰指令与吹灰需求不匹配引发的排烟温度上升、烟道阻力增大、炉膛严重挂渣、掉渣或受热面管壁吹损减薄等安全、经济性问题,中心开发了智能吹灰控制平台。
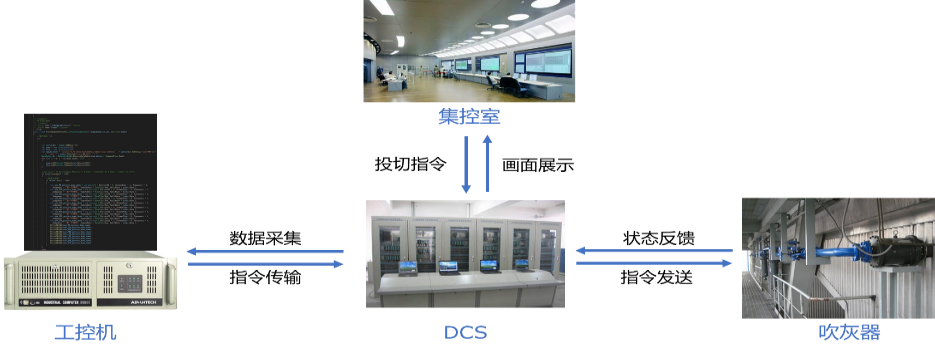
技术特点:
1、 通过融合数据挖掘和机理模型建立了多维度约束智能吹灰控制系统,实现了吹灰器的按需控制。
2、 建立了基于传热理论、流体力学理论及数据挖掘的受热面灰污监测模型,对监视电站锅炉受热面的清洁程度提供了有力手段。
3、 基于不同受热面壁温、受热面洁净因子吹灰器敏感性分析,掌握了各吹灰器的敏感性,并以此对吹灰器进行了分组。
技术优势
1、 因面制宜,按需吹灰,针对不同受热面的传热特性,建立了鲁棒的受热面灰污监测模型。
2、 粗中有细,精确分组,针对复杂的炉内工况,对吹灰器吹灰效果制定差异化的吹灰频率。
3、 智能监盘,操作简单,系统实现对受热面运行数据的智能分析,减缓运行人员监盘压力。
工程示例(某电厂350MW机组智能吹灰项目)
智能吹灰系统界面:
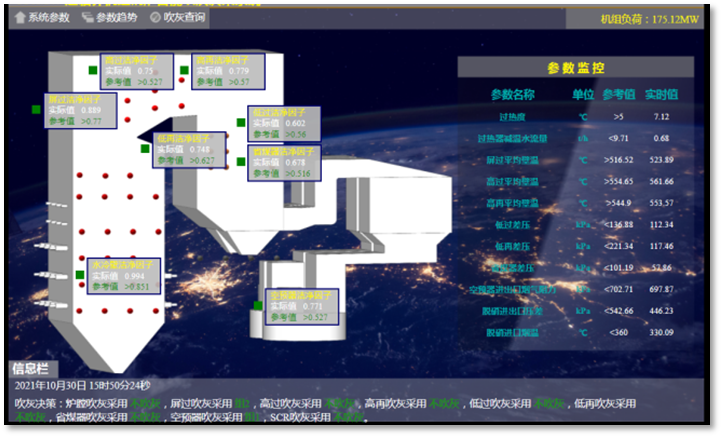
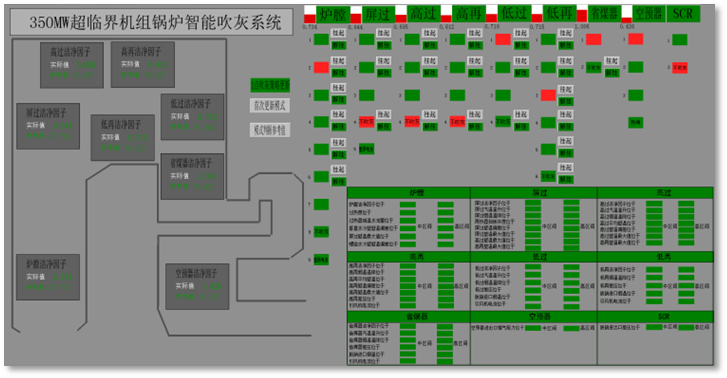
智能吹灰系统投运后,吹灰蒸汽消耗降低至876-1208 吨/月,平均每月1063吨,按原有吹灰策略,锅炉蒸汽消耗量约为2014 吨/月,较原有吹灰策略节约蒸汽47.3%。由于减少吹灰蒸汽耗量可节约标煤约1300吨/年,减少二氧化碳排放3444吨/年。同时,系统投运期间锅炉排烟温度没有上升,表明受热面积灰或结渣情况没有恶化。
系统投运后显著减少了由于“垮焦”带来的受热面管壁超温现象,月均超温时间由47.3分钟降低至14分钟,降幅达70%,有效的延长了管壁使用寿命,有利于减少机组检修时的维修和费用,提高了锅炉生产运行的安全性。